Right now, we’re welcoming a new area of manufacturing. It’s a shift where machines are no longer just tools to assist workers but are instead becoming intelligent collaborators in the production process. This is what we call a smart factory.
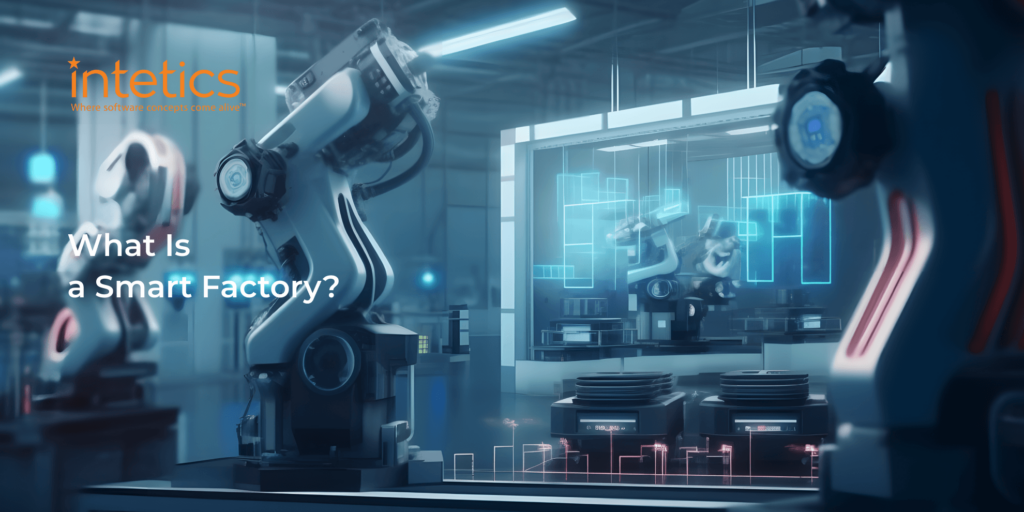
Smart factories are the result of the fourth industrial revolution, also known as Industry 4.0. And it’s only the beginning. According to Precedence Research, the global smart factory market is now valued at over $129 billion and will reach close to $322 billion by 2032. But before that happens, more organizations need to understand what it is and how it reconstructs the manufacturing process, and you’re at the right place to learn about it.
This article will answer some of the most common questions and give you some practical advice on how to begin your transformation.
How Does a Smart Factory Work?
A smart factory operates by integrating various technological components and data management systems into a unified digital ecosystem. In a traditional factory, they use automation and robotics in isolated parts of their operations. A smart factory is different in a way that it interconnects machines, people, and data management systems.
The key feature of a smart factory is its ability to learn and improve from experience. It’s like a living organism that can self-optimize and self-correct, always striving to be better and more resilient.
Imagine a factory that can diagnose and fix problems on its own without the need for human intervention (or only minimal intervention) — or a factory that can predict machine failures before they occur and schedule maintenance proactively. This is what smart factories and the people behind them are aiming for.
Structure of a Smart Factory
At the heart of a typical smart factory is a sophisticated structure that enables data acquisition, analysis, and intelligent automation. Let’s take a closer look at each of these elements:
Data Acquisition
It all starts with data acquisition, which is collecting critical information from multiple sources within your manufacturing environment. From your machines and sensors to the special equipment you use in your factory, all these sources hold valuable data. The way you extract that data may vary from RFID tags that track the movement of materials to machine-to-machine communication that gathers data from multiple devices simultaneously.
Once this data is collected, it’s stored in a centralized database, the beating heart of the smart factory’s operations.
Data Analysis
Data analysis is the next step. During this stage, the data collected from multiple sources is put under the microscope and analyzed using advanced algorithms and machine learning techniques.
This analytical approach unlocks valuable insights, helping manufacturers identify patterns, trends, and other critical information. Further on, these insights will be used to optimize production processes and make informed decisions.
Intelligent Automation
The final piece is smart factory automation. This means connecting cutting-edge technologies like artificial intelligence and robotics to create an improved production environment. The choice of what should be automated is up to you. It can be something on the simpler side, like material handling tasks, or something more complex, like quality control and predictive maintenance processes.
Effect of IoT on a Smart Factory
Internet of Things technologies have brought significant transformation to smart factories, particularly in three dimensions: shop floor and field operations, manufacturing supply chain, and remote and outsourced operations.
- Within shop floor and field operations, IoT technologies provide advanced visibility and control over company resources. They can meet the demands that manufacturing execution systems and enterprise resource planning software cannot. Moreover, this all can be done in real time.
- IoT-enabled supply chain management solutions also excel at real-time information. And now, manufacturers can quickly identify and resolve any issues before they escalate. This prevents the loss of goods, ensures timely delivery, and helps prevent disputes.
- In remote and outsourced operations, IoT mitigates numerous challenges: greater demand for customization, increasingly complex supply chains, lack of local talent, and more. For example, managers in California can view the operating and condition parameters of their manufacturing affiliate in Texas (temperature, vibration, rotation speed, etc.).
Interestingly, the effect of IoT on smart factories has been underestimated. In 2015, McKinsey made a bold prediction (at the time) that the improvements in manufacturing brought by IoT could be worth more than $470 billion per year by 2025. But it turns out, it’s much more than that. In a recent report, they’re saying the value could reach an astounding $5.5 trillion to $12.6 trillion globally by 2030.
Benefits of a Smart Factory
If you’re a business that’s considering a smart manufacturing initiative, you’re probably interested in the advantages that come with it. In short, it brings about a new era of efficiency, agility, and flexibility.
The long answer is the following list of benefits:
Increased Efficiency
Next-gen factories can optimize processes quicker than ever, which translates to reduced downtime, increased output, and enhanced productivity. Moreover, automation frees up human workers to focus on more complex and creative tasks. Not only does it create a more satisfying working environment, but it’s also a more efficient use of human capital.
Improved Quality
By using cutting-edge technologies, smart factories can catch potential issues before they become full-blown problems. So, manufacturers can be confident that items are produced to the highest possible standard. This means fewer defects, less waste, and ultimately happier customers.
Improved Safety
A smart factory essentially provides every worker with a personal assistant, constantly providing them with real-time guidance and information to keep them safe. This assistant comes in the form of sensors and trackers. And thanks to automation, workers are not needed for dangerous or repetitive tasks that can put their safety at risk.
Flexibility
Smart factories can adapt to changing product designs and specifications, thanks to the flexibility of 3 additive manufacturing techniques. This means that manufacturers can quickly iterate on product designs and make changes on the fly. And the best part is that it can be done without having to retool or redesign the entire manufacturing process.
Cost Savings
Cost savings come in three forms: raw materials, labor, and energy. Optimized production processes reduce waste and save on raw materials, while automation and predictive maintenance techniques reduce labor and maintenance costs. As for energy, smart factories tend to use high-efficiency lighting, heating, and cooling systems, as well as energy-efficient machinery and equipment.
Competitive Advantage
An astounding 86% of manufacturers in the US believe that smart factories will be the main driver of competition by 2025. This statement seems to be true: smart factories are already demonstrating their ability to provide a competitive edge over traditional manufacturing processes. After all, advanced technologies and data-driven decision-making is a powerful combination.
Technologies Used in a Smart Factory
Smart factory solutions are a testament to the power of technological integrations. This type of achievement could never be done with just one technology or without a high level of collaboration and cooperation between departments. So, why not take a look at the complex network of devices and systems involved here?
Cloud Computing
Cloud computing serves as a conduit that facilitates the flow of data and information across the entire factory. Whether it is public, private, or hybrid, the cloud is designed to be accessible from anywhere in the world. So, this provides the necessary infrastructure for the global connectivity you need.
Anytime you need to access data or applications, the cloud will make it readily available. For example, a remote worker needs speed and energy usage data on a machine in a smart factory, they can view it through a cloud-based application, like a dashboard or a mobile app.
Another significant advantage of using cloud computing is its seamless integration with other technologies, which we’ll cover below.
Edge Computing
While cloud computing gives you a centralized platform for data and application management, edge computing brings processing power and intelligence closer to where data is generated. Essentially, part of the job will be done directly on the factory floor.
For example, there is a machine equipped with sensors that monitor its performance. These sensors can generate vast amounts of data, which is analyzed in real time on the machine itself. You’re only using local computing resources in that case. So, you’re not waiting for data to be sent to a remote cloud server for processing.
Industrial Internet of Things
If you’ve heard of IoT, IIoT should be a familiar concept. IIoT encompasses the network of physical devices, vehicles, and other items embedded with sensors, software, and connectivity. Together, this enables them to collect and exchange data. The difference is that IIoT specifically refers to devices within an industrial setting.
In a smart factory, this level of connectivity allows for a high degree of automation and control, as well as real-time monitoring and analysis of the production process. For example, IIoT can monitor the humidity of storage areas to prevent moisture damage to raw materials or finished products. Everything from food to electronics can be affected (mold growth, spoilage, bacterial contamination, etc.).
Robotics (+ Cobots)
Robotics and cobots (short for collaborative robots) are becoming increasingly prevalent in smart factories. They can be integrated into initial stages like assembly and material handling, as well as later stages like quality control and packaging.
One of the best things about robotics is their ability to perform repetitive and dull tasks. But cobots take it a step further. They work alongside human employees, performing tasks that are too dangerous or physically demanding for humans to do on their own. This not only improves safety but also frees up employees to express human ingenuity in other areas.
Machine Learning
Think of it this way: if your factory were a living organism, machine learning would be its brain. It can process massive amounts of data from all over the factory, identify patterns and trends, and learn from its mistakes. It can predict when materials are about to run out, detect quality issues before they become a problem, and even optimize your supply chain.
Without ML, it’s hard to identify areas of inefficiency and suggest improvements to the supply chain. It’s possible but also laborious and very time-consuming. And by the time traditional systems catch up, it may be too late, and opportunities for improvement may have been missed.
Big Data Analytics
Connected devices and sensors generate vast amounts of data, and if you’re capable of analyzing all of it, the potential insights and optimizations are truly limitless. You can do everything from identifying bottlenecks in the production line to understanding customer needs and preferences.
One of the possible uses is predicting and preventing equipment failure. For this, you’ll need the previously discussed technology—ML—to detect patterns and anomalies in the data. The models will analyze data from multiple sources, like temperature sensors and production output, and predict when a machine is likely to fail. As a result, maintenance teams will be more equipped to take proactive measures.
3D Printing
3D printing is not just a cool technology for creating small trinkets. It’s a manufacturing game-changer that opens a world of possibilities for creating customized and unique products.
In a smart factory, 3D printing technology can produce spare parts on demand. As a result, it reduces the need for extensive inventory and minimizes downtime. This means that if a critical part of a machine breaks down, you can replace it quickly without having to wait for a new one to be ordered and delivered.
You can also easily change your products with 3D printing. Perhaps you have an idea to create complex geometries that would be impossible with traditional manufacturing methods. Well, now you can turn those ideas into reality.
Digital Twins
A digital twin is a virtual replica of your factory, with every detail and process meticulously modeled. If you have one, you can run simulations and analyze data to predict how your factory will perform. It can be applied to physical products, processes, or even entire systems.
Let’s say you’re producing a complex piece of machinery that requires frequent maintenance. With this piece of technology, engineers can simulate how it will perform under real-life conditions. If they find out a particular component will experience excessive wear and tear, this can be addressed and prevented on the real machine.
Virtual Reality and Augmented Reality
Imagine a technician getting ready to repair a complex piece of machinery. In the past, they would have to rely on trial and error, taking apart the machinery and putting it back together. They would just hope they got it right. But with VR technology, they can now practice their repairs in a safe and controlled environment.
As for AR, consider training workers on the factory floor. Instead of reading through manuals or watching videos, they will use AR to learn how to operate machinery, assemble products, and perform maintenance tasks. So, you’ll be able to speed up the process and possibly cut expensive and time-consuming training programs.
How to Begin a Smart Factory Transformation?
Are you ready to get into careful planning and execution? If so, here are some steps you can take to begin this transformation:
- Define your goals and objectives. Perhaps you’re struggling with production bottlenecks or inconsistent product quality. Maybe you’re looking to reduce waste or improve safety on the factory floor. Make sure to define the metrics you will use to measure success.
- Assess your current infrastructure and technology. Ask yourself: How are we collecting and storing data? Are we able to analyze that data in real time? Do we have the necessary connectivity to support a more advanced smart factory infrastructure?
- Develop a roadmap. This plan should include all the technologies you’ll need to implement, the required investments, timelines, and potential risks. As you create your roadmap, remember to prioritize the steps based on their potential impact and feasibility.
- Build a cross-functional team. Assembling a team with the right mix of skills and experience is crucial. This may involve bringing in new talent or partnering with external experts who can provide what you need.
- Select the right technology. As you’ve seen from the section above, there is a wide range of technologies to choose from. The key is to select the technologies that align with your goals and infrastructure. For example, if you’re looking to reduce defects, consider sensor technologies.
- Implement and integrate. It may involve upgrading hardware, installing new software, and configuring systems to work together seamlessly. And if you’re working with a partner, you’ll need to establish clear communication channels.
- Monitor and optimize. For example, you may discover that certain machines or processes are causing delays or wasting resources. With this information, you can make adjustments to improve the flow of production and reduce waste.
Just a word of caution: implementing smart factory technologies can be a costly and complex undertaking. Also, managing and analyzing large amounts of data, protecting against cyber-attacks, and retraining the workforce can all be challenging.
But these efforts serve the bigger goal, which does pay off. And by working closely with technology partners and team members, you can address these challenges and accelerate the smart factory transformation.
With the end-to-end Smart Factory solution by Intetics, hundreds of electronics manufacturing, automation machinery manufacturing, biomedical, pharma manufacturing, cosmetics & beauty companies enhance their factory, warehouse, and other core processes. Let’s talk today and discover how your business can reach fully automated and efficient operations with minimized downtime and maximized equipment productivity.