In 80% of the cases, large construction projects cost more than originally estimated. Also, projects take, on average, 20% more time due to schedule delays. The most common reasons are fairly simple: design and topography errors, conflicting information, poor site planning, etc.
But in reality, all these factors stem from one main reason – insufficient use of innovative technologies. According to McKinsey, <1% of revenue is used for R&D spending in construction companies; the same metric in the auto industry can be as high as 4.5%.
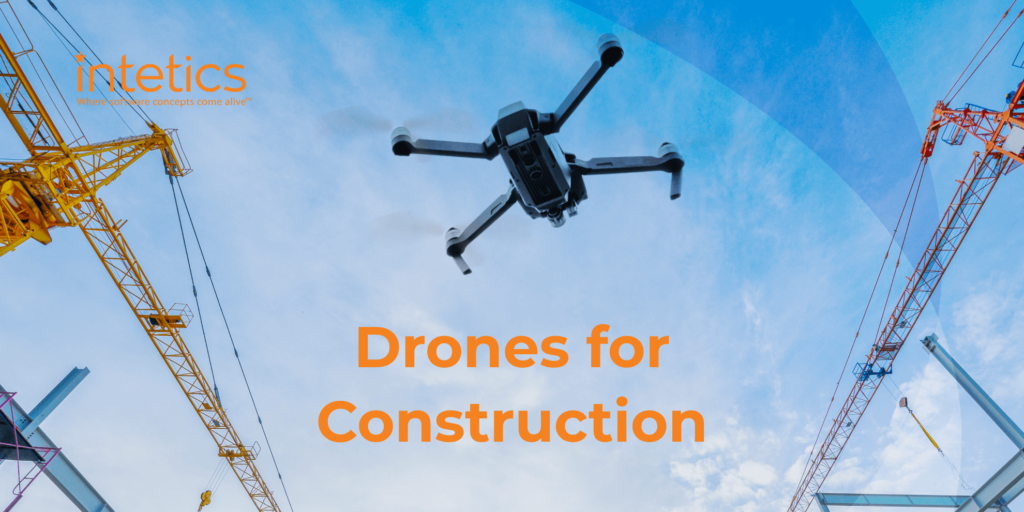
Construction companies, while generally having some of the most conservative attitudes towards technology, are nevertheless actively introducing drones into their operations. According to USG and the U.S. Chamber of Commerce, 63% of contractors are already using drones in construction projects.
And it’s not just a matter of mandatory monitoring of construction sites for workers’ safety. At a construction site, drones are useful at all stages – from preliminary assessment of site suitability to the maintenance of finished objects.
What Drones Do Better Than Humans on a Construction SiteQuickly conduct a topographic survey of the site
1.Quickly conduct a topographic survey of the site
Aerial photography helps create the most accurate 2D and 3D maps with geolocation and geodetic information (distance, elevation, elevation difference, etc.). Those can later be used to accurately estimate excavation volume or the quantity of soil for filling, choose the best placement for objects, and store building materials.
The collected data can also be used to create architectural and design projects, presentations for investors. 3D models, compiled according to all terrain attributes, can showcase everything: how buildings will cast shadows, where to plan parking or landscaping, and optimal placement of solar panels and collectors.
All you need to do is a drone and an operator. In good weather conditions, the device can work all day, returning to the base for a battery change every 40-60 minutes. One drone replaces an entire team of surveyors and a helicopter combined while also being much cheaper.
2. Accurately record the project progress
A drone is suitable for assessing how the factual results correspond to the plan based on a repeated series of surveys. This allows for more efficient project planning, up-to-date reports, and quicker dispute resolutions with contractors.
At construction sites, the actual rate of construction often differs from the plan and may not match what the field crew reported. And since all processes are connected to each other, if one thing fails, for example, monolithic construction, it might cause delays in communication or disruptions in building materials.
Drones also help estimate the amount of work for piecework payments. How can you calculate exactly how much soil was dug up and removed from the site? By weighing every truck? There is a better option: you can place points with geospatial information on the detailed pictures of the construction pits. Those can be used as a basis to accurately calculate the volume of soil taken from pits and trenches. A similar approach is suitable for calculating dimensions of foundations, walls, floors, rafter systems, etc.
3. Share up-to-date data promptly
One person would need several days to shoot a large construction site from different angles. In the meantime, some things might change and require additional shots. If necessary, drones make it easier to update the site map on a daily basis and even monitor the processes in real-time.
Where Can You Save Money by Using a Drone on a Construction Site?
- Design. 3D maps of the area allow you to create projects of future buildings faster and more accurately than when you work with on-field surveyors.
- Settlements with contractors. They will be as accurate and fair as possible since they’re based on what was actually carried out. A drone helps you record volumes, timing, and the rate of construction.
- Geodetic surveys. A drone can accomplish a task that would take people 2-3 weeks in 2-3 days.
- Creating presentations and reports for investors and clients.
- Walking tours on the field. You can spend less time on planned routine examinations and on eliminating impact from emergencies (because you can spot them immediately or prevent them).
- Manual examinations. A drone does not need any belay devices or personal protective equipment. It has no problem shooting angles that a person with a total station and a tape measure couldn’t ever do.
- Document digitization. A bit of conservatism is helpful when it comes to safety and accuracy. But outdated formats like paper drawings, projects, estimates, logs, and reports just slow down the construction process. Drones help you start to digitize terrain maps, visual reports, and image-based drawings. This helps you analyze and share data faster.
- Maintenance of finished objects. Drones are useful for inspecting roofs, engineering units, ceilings, structural supports, etc.
- Subsequent projects. No objects are the same, but there are typical and similar ones. After estimating the amount of work for one object and comparing the estimates with actual results, you can rely on this data for other projects.
Lidar, GPR, PTZ cameras – these are your new employees. They will never get tired or go on vacation during a peak season.
We should also point out that drones with additional attachments can help directly in the work process: pull electrical cables at a height and deliver tools. At some point in the future, human interference will only be required at the very end of construction – to get access keys to the robot cleaner. It won’t be soon, so, for now, let’s start with just drones!
Find more about Drones :
Download The New White Paper:
- The Ultimate UAV (Drones) Technologies Overview by Tech Geeks