Picture this: a manufacturing plant running like a well-oiled machine, every cog and gear turning in perfect harmony. Suddenly, one machine fails, and the entire production process grinds to a halt. That’s where predictive maintenance comes in — the champion of maintenance strategies, capable of anticipating and identifying potential equipment failures before they occur.
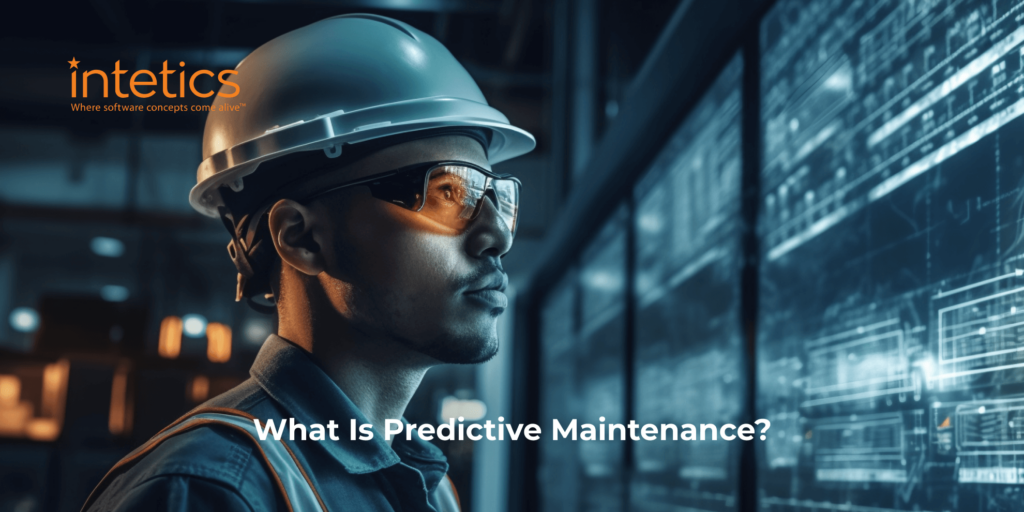
Deloitte reports that having such a crystal ball for your machinery gives you the power to increase productivity by 25%, reduce breakdowns by 70%, and lower maintenance costs by 25%. So, why wait for a breakdown to happen? You can stay one step ahead with predictive maintenance.
Featured material: Predictable and Cost-Effective Manufacturing Operations with Predictive Maintenance
Definition of Predictive Maintenance
Predictive maintenance uses sophisticated data analysis and machine learning algorithms to predict potential equipment failures. By constantly monitoring crucial performance indicators (pressure, noise, flow rate, etc.), algorithms can spot anomalies or patterns that suggest trouble is brewing. It’s like always having someone on the lookout for signs of potential failure.
With such an approach to maintenance, businesses can stay ahead of issues instead of dealing with unexpected breakdowns as they arise. For example, a production line in a factory experiences a sudden breakdown due to a malfunctioning pump. Without predictive maintenance, the issue may go unnoticed until the pump fails completely, causing significant downtime and lost productivity. However, with predictive maintenance, the anomaly in the pump’s performance can be detected early.
Why Is Predictive Maintenance Important to Today’s Businesses?
In today’s fast-paced business world, companies are facing unprecedented levels of competition and change. Thanks to the Amazon Effect, customers are expecting more control, personalization, and speed in their interactions with businesses. This has put pressure on businesses across industries to keep up with these high expectations, leading to challenges in maintaining affordable supply chains and manufacturing relationships.
To add to these challenges, the trade and political climate has become increasingly uncertain and volatile. Together, these factors have made it more important than ever for businesses to be agile and adaptable in order to survive and thrive. As a result, business leaders are turning to innovative solutions, predictive maintenance included, to gain a competitive edge.
Predictive maintenance is one of the most promising solutions for modern businesses, especially for those with high-value assets and large, complex operations. But it’s not just for large corporations with massive operations. Small and medium-sized businesses can also take advantage of this technology, as it has become more accessible and cost-effective than ever before.
What Is the Difference Between Reactive, Preventive, and Predictive Maintenance?
Reactive maintenance, also known as “run to failure,” is the simplest and most basic type of maintenance strategy. It involves waiting until a component or system fails before acting. While reactive maintenance can be appropriate for low-risk systems, it has several disadvantages. Mainly, it can lead to unexpected downtime and repairs and increase the risk of safety incidents or environmental hazards.
Preventive maintenance vs. predictive maintenance is a bit more nuanced. Both strategies are proactive in nature, but they differ in their approach and the level of precision involved.
The first one, preventive maintenance, involves scheduling routine maintenance tasks at predetermined intervals. But this happens regardless of the condition of the equipment. For example, a company might schedule a technician to inspect and lubricate a machine every six months, and it doesn’t matter how much it has been used. While this approach does help identify and address potential issues before they become serious, you’re also running the risk of having unnecessary maintenance tasks and expenses.
The other one, predictive maintenance, takes a more data-driven approach. In this case, you’re collecting and analyzing data on equipment performance, usage, and other factors. You’re informed on the potential issues by predictive maintenance algorithms. Here, a sensor might detect that a machine is operating at a higher temperature than usual. So, even if no one schedules a maintenance check, the appropriate personnel get the alert and checks out the machine.
How Do Predictive Maintenance and IoT Analytics Work?
These cutting-edge technologies use a combination of advanced techniques to keep your equipment in tip-top shape. They’re doing it by sensing, gathering, transmitting, analyzing, and taking action based on data related to the machine’s performance and health:
Sensing and Gathering Data
With advanced sensors like thermal imaging and vibration sensors, you can rest assured that your equipment is being monitored 24/7. Any changes in temperature, vibration, sound, and any other parameter that could indicate a potential issue are monitored.
Transmitting Data
The data collected by sensors is then transmitted in real time across the network to a central business system. This means that people with the needed permissions can remotely monitor the equipment’s performance and health status. But more importantly, transmitted data arrives at intelligent systems for analysis.
Applying Intelligent Technologies
This is where everything comes together. The data collected and transmitted at the previous stages is analyzed using intelligent technologies. Now, the goal is to detect patterns, anomalies, and correlations that might be missed by the naked eye. This allows you to gain a deeper understanding of what is going on with your equipment.
Taking Rapid Action
Based on the insights gained from the data analysis, the business establishes maintenance and response protocols. These protocols can include both human and automated responses. For example, if the system detects that a certain parameter has exceeded a certain threshold, it can automatically trigger a shutdown. Alternatively, you can schedule a maintenance appointment.
Overall, you have the flexibility to choose the approach that works best for you.
Monitoring Asset Conditions and Leveraging Predictive Maintenance Technologies
The first crucial step for an organization is identifying the conditions that need to be monitored for each machine. The second is leveraging the right technology so that their predictive maintenance tools can analyze data from those conditions and deliver actionable findings.
What Conditions to Monitor and How
What are the specific conditions that need to be monitored for each machine? Managers can use a variety of analysis methods, including visual, auditory, thermal, or a combination of criteria, to determine them. Once these conditions are identified, you need to determine the correct sensors that will perform the actual task of monitoring.
One popular predictive maintenance technology is vibration analysis. It can detect small changes in vibration patterns, thus indicating imbalance or misalignment. Similarly, sound and ultrasonic analysis can detect changes in sound patterns, while fluid analysis provides information about coolants and lubricants.
You can also opt for specialized tools designed for industrial needs. For example, laser alignment, electrical circuit monitoring, crack detection, corrosion monitoring, and electrical resistance changes are all useful in their own unique ways.
What Technologies to Use Next
Fitting assets with the appropriate sensors and monitors are not enough to truly make a difference. You also need to connect them to a central business system via a cloud connected IoT network. From there, advanced AI-driven software solutions take over to perform complex analytics and deliver insights.
But what exactly does this process involve? It starts with creating an IoT network, which allows assets to send and receive data in real time, and for older assets, you’ll need to fit IoT gateway devices. The process then utilizes cloud connectivity to integrate multiple data centers into a single database and system.
Next, AI and machine learning come in to learn from data and new experiences over time. You can take it a step further with digital twins, or virtual recreations of physical assets. They augment predictive maintenance by providing a platform for machine learning and AI tools to learn from experiences that have not even occurred in real life yet.
In What Industries Predictive Maintenance Can Be Used?
Predictive maintenance solutions can be helpful in any industry that deals with some sort of equipment, especially if it’s critical for their operations.
Here are a few use cases to consider:
Manufacturing
Manufacturing is a vast industry, with predictive maintenance finding applications in various equipment and processes. Take food and beverage manufacturing, for instance. A manufacturer of bottled beverages can use sensors to monitor the performance of their filling machine. By using sensors for changes in vibration, temperature, or pressure, they can schedule preventative maintenance, as well as reduce the risk of contamination and ensure consistent filling levels.
Or in the pharmaceutical industry, you can monitor equipment used in the manufacturing process, such as tablet presses, mixers, and packaging machines. This can prevent delays in the delivery of life-saving drugs.
Oil and Gas
In offshore drilling, companies can use predictive maintenance solutions to monitor their drilling equipment: drill bits, motors, and pumps. In this industry, equipment failure and unscheduled downtime can cost millions of dollars in lost production and maintenance expenses.
Another example is in pipelines. Pipeline leaks can have severe environmental consequences, and detecting and repairing them quickly is crucial. With the right solutions, sensors can detect changes in pressure and flow rates, alerting maintenance teams to take corrective actions before a leak.
Transportation
In transportation, critical equipment can include engines and transmissions in vehicles, airplanes, and trains. For example, airlines can use sensors for their aircraft engines to detect any abnormalities in vibration, temperature, or other factors. By analyzing this data, they can schedule maintenance before any issues occur, reducing the risk of costly delays or cancellations. Similarly, shipping companies can use predictive maintenance for their vessels’ engines and avoid unexpected breakdowns while at sea.
Featured material: The Ultimate UAV (Drones) Technologies Overview by Tech Geeks [White Paper]
Healthcare
An example of predictive maintenance in healthcare is monitoring medical equipment like MRI machines, X-ray machines, and CT scanners. These machines are critical for diagnosing and treating patients, and any downtime will affect patient outcomes.
The same approach can be applied to hospital infrastructure like HVAC systems and backup generators. It’s crucial that the hospital is always operational and prepared for emergencies. So, taking proactive measures for the hospital’s infrastructure equipment is definitely a good idea.
Energy
Take wind turbines, for example. With real-time monitoring of critical components like the gearbox and rotor blades, you can identify when bearings are starting to wear out and schedule maintenance before they fail. You just need to monitor their vibration and temperature.
Or you can keep an eye on the output of solar panels and see when they are starting to degrade. With simple cleaning and repairing, you can improve their efficiency and increase the amount of electricity generated from renewable sources.
Agriculture
Predictive maintenance can help farmers keep their equipment in optimal condition for the right time that their crops need to be harvested.
It can also help with precision agriculture, which involves using technology to optimize farming operations, such as sensors that monitor soil moisture, nutrient levels, and weather conditions. Since farmers ensure that they are functioning properly, they receive accurate data for informed decision-making about when to plant, irrigate, and harvest crops.
Benefits of Predictive Maintenance
At this point, you already have a general idea of how this approach can help businesses improve their operations and bottom line. But let’s dive deeper into the specific advantages of predictive maintenance:
Reduced Downtime
Predictive maintenance reduces the risk of unscheduled downtime and minimizes its impact on operations. This is because you’re scheduling maintenance or repairs before a breakdown occurs. Basically, your equipment is never out of operation (unless it’s time to upgrade to a better piece of machinery).
Increased Equipment Lifetime
Remember: you’re addressing issues before they turn into larger problems. This means that equipment is less likely to break down, which ultimately extends its overall lifespan. Plus, your equipment will always be operating at its optimal level, reducing wear and tear on individual components.
Cost Savings
The first bout of cost savings is associated with the elimination of emergency repairs and unplanned downtime. The second bout round comes from reducing labor costs and eliminating unnecessary parts replacement. Indirect cost savings are the third—by ensuring that equipment is operating at maximum efficiency, you can reduce energy waste and lower your energy bills.
Better Productivity
Predictive maintenance has a ripple effect throughout a business. Workers can spend more time focusing on their tasks and less time dealing with equipment issues. And when machines are running at peak performance, it often produces higher-quality output, further boosting productivity.
Improved Product Quality
With well-functioning machines, businesses can produce goods that are consistent, reliable, and of higher quality. This not only leads to increased customer satisfaction but also helps to build a positive reputation in the market.
In industries where quality is of utmost importance, such as food and beverage, pharmaceuticals, and automotive, predictive maintenance can make a huge difference.
Final Thoughts
In conclusion, predictive maintenance is a game-changing approach to asset maintenance that can help businesses optimize their operations, reduce downtime, and save money.
However, implementing a predictive maintenance strategy requires a shift in mindset and approach. Many businesses have been using the same maintenance strategies for decades. It’s often true even if other areas of their operations have been modernized with new technologies and practices.
Adopting a predictive maintenance approach requires a team effort and a willingness to break old habits. But don’t worry; you don’t have to do it alone! Partnering with a software vendor can help you unlock the full potential of predictive maintenance and propel your digital transformation journey forward. Let’s talk.