Manufacturing companies are always looking for ways to improve their operations and drive efficiency. One European automobile maker, for example, installed a touch device with apps at each workstation, which helped guide real-time problem-solving. The results were impressive: the company saw a 40% increase in accomplishing tasks correctly on the first pass.
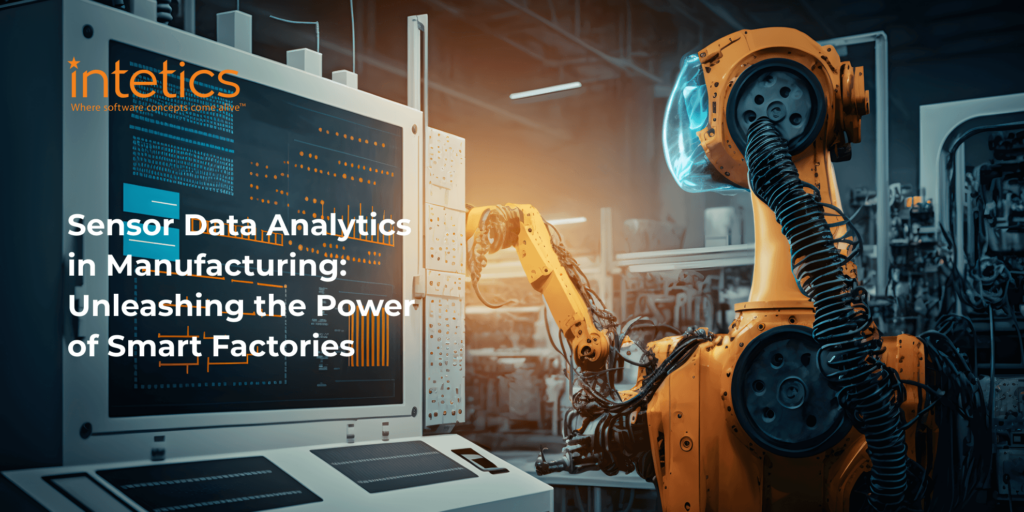
This is just one example of the power of sensor data analytics in manufacturing. If you’re a manufacturer, there are many ways to benefit from leveraging the technology. So, join us as we delve into the topic and explore some of the other key applications.
Read also: What Is a Smart Factory?
What Is Sensor Data?
Sensor data is information collected by devices that detect and measure changes in the physical environment. They collect data around them and send that information to a computer or another device for analysis. For example, in a home environment, you can set up a motion sensor that turns on the porch light or sends you a notification on your phone.
In the manufacturing environment, the most common types of sensors used include:
- Temperature sensors for materials and equipment
- Pressure sensors for gasses or liquids in various manufacturing processes
- Flow sensors to measure the rate of flow of liquids or gasses
- Proximity sensors to detect the presence of objects, e.g., on a production line
- Vibration sensors to monitor the condition of equipment and detect any small changes in movement.
Featured Case Study: IoT-Based Air Monitoring System Identifies the Sources of Poor Air Quality Across 6 Offices Globally With 3,500 Events Daily
Technologies Used for Processing and Analyzing Sensor Data
To process and analyze data from sensors, organizations are using a combination of technologies. First, data collection and storage are key components, and this includes the sensors themselves, as well as storage in a database, data warehouse, or data lake.
Another important technology is the Internet of Things, which enables sensors to communicate with other devices and systems. This connectivity allows for seamless and efficient transmission of data. Then organizations are turning to artificial intelligence and machine learning to analyze the data and identify patterns and anomalies that might not be immediately apparent.
In addition, edge computing moves data processing closer to where it is collected, while cloud computing helps organizations achieve greater scalability and flexibility than on-premises systems.
Benefits of Sensor Data Analytics in Manufacturing
Having an extra set of eyes and ears in the form of sensor analytics improves the manufacturing process in the following ways:
- Improved process efficiency. It becomes easier to identify bottlenecks, inefficiencies, or areas for improvement.
- Enhanced product quality. By catching issues early, manufacturers can adjust product quality and consistency.
- Reduced downtime and maintenance costs. Sensors help monitor equipment and predict when maintenance is needed, so organizations can shift to a proactive approach.
- Energy conservation and waste reduction. Manufacturers can identify more opportunities to reduce their environmental impact and save on costs.
- Increased worker safety. Sensors can alert workers to potential hazards, preventing accidents and improving overall conditions in the workplace.
Applications of Sensor Data Analytics in Manufacturing
With the days of relying solely on human intuition and guesswork gone, the power of sensor data processing comes into play in the following areas:
Predictive Maintenance
Identifying equipment anomalies is a critical aspect of predictive maintenance. By using sensor analytics, manufacturers can monitor the health of their machines and detect any deviations from normal operating conditions. This can include changes in temperature, vibration, or other key performance indicators. For example, you won’t miss a sudden drop in the hydraulic pressure in your equipment.
Scheduling maintenance tasks is another important area. This can involve using predictive models to forecast when equipment is likely to fail based on historical data. Or it can be analyzing sensor data to run checks and perform repairs before it causes a breakdown.
Quality Control and Assurance
Thanks to real-time monitoring of product quality, manufacturers can adjust and ensure the product meets the desired quality standards. For example, a pharmaceutical company may notice an increase in temperature. As they identify the source of the problem in time, they act before the product is compromised.
Similarly, you can identify deviations from normal operating conditions or detect defects in the final product. Whether it’s the shape of a component or the chemical composition of a product, sensors and algorithms can alert you.
Process Optimization
Another capability that sensor data analytics opens for manufacturing is process optimization, i.e., identifying bottlenecks, inefficiencies, and opportunities for improvement.
Let’s take measuring the time it takes to complete a specific task or monitor the flow of raw materials through the production line. You may find where the process is slowing down. In the first case, sensor analytics may tell you that there is a machine malfunction or manual error. In the second scenario, you may find that certain raw materials are being used more quickly than others.
Energy Management
As for energy management, organizations can reduce energy usage and lower costs. If there is an inefficiency in the energy consumption of individual machines or production lines, you will know. Real-time data will be matched against normal consumption patterns and let you know when to take corrective action.
You can also get some help with energy-saving measures. For instance, automate the shut-off of machines or equipment during periods of low production or when not in use.
Worker Safety and Monitoring
And finally, when it comes to worker safety, manufacturers are taking a proactive approach with the help of sensor data analytics. As a result, workers receive better protection from harm while on the job.
If you’re operating a facility where air quality is a concern, you can use sensors to keep track of ventilation and air filtration systems, as well as the amount of the amount of particulate matter (with an infrared device). Or you can monitor worker fatigue and alertness levels, which will help you identify when workers are at risk of fatigue-related accidents.
Challenges and Considerations in Implementing Sensor Data Analytics
Before you introduce sensors into your organization, it’s important to consider the challenges and potential roadblocks you may face along the way. They fall broadly into three categories:
- Data quality and management
- Technological challenges
- Workforce challenges
Data quality and management can be challenging, as sensors are affected by environmental conditions, and this leads to inaccurate readings. A possible solution to this is implementing data validation and cleansing techniques. Another issue under the same umbrella is the need to ensure data protection from unauthorized access or breaches.
As for tech challenges, the integration of disparate systems and the scalability and flexibility of solutions are both worth mentioning. The first can be solved by standardizing communication protocols and technologies across different systems and devices. And the second — by using cloud-based solutions that can scale up or down based on demand, as well as implementing agile development methodologies.
Finally, workforce challenges require employees that are trained and knowledgeable in analytics. Partnering with external experts usually helps bridge this gap. Overall, changing the culture to embrace data-driven decision-making should be a concerted effort from all levels of the organization.
Real-World Examples of Sensor Data Analytics in Manufacturing
Robert Schmid, IoT Chief Technologist at Deloitte Digital, shared an interesting case study regarding the implementation of data-collecting sensors for location tracking. The sensors were used on equipment for one of his clients. The equipment was stored on a massive inventory lot that was three-quarters of a mile on each side, which made it difficult to find specific items. With location-tracking sensors, the client saved $3 million per year on each of its production lines.
Another example comes from Dr. Richard Soley, Executive Director at the Industrial Internet Consortium. One of the IIC’s testbeds involved a client with a large number of tools that were constantly getting misplaced. The client found that its workers spent 47% of their time searching for the right tools. However, thanks to the IIoT solution, workers were told exactly where the tool they needed was located.
Trends and Opportunities in Sensor Data Analytics
One of the most exciting areas of development is that sensors are becoming smarter, more efficient, and more versatile. As technology advances, it’s opening up new possibilities for data-driven decision-making and process optimization.
The emergence of edge devices is also interesting. We’ve already talked about edge computing, but it’s worth emphasizing what a game-changer it is for manufacturers. And it’s only going to grow bigger.
Another impressive development is the growing use of virtual or soft sensors. These can complement physical sensors and provide a more comprehensive view of the manufacturing process. The trend also ties into the fusion of multiple sensors.
Biosensors, which can measure biological or chemical responses, are also becoming more mature and could impact the industry. For example, manufacturers can use biosensors to monitor the health and well-being of workers. These sensors can also detect the presence of harmful bacteria or other contaminants in food products, along with other applications.
Conclusion
The ability to collect and analyze data in real time from a wide range of sensors may be the difference between success and failure in the modern manufacturing industry. However, manufacturers must take a strategic approach to fully realize this potential. This means using the right technologies, building a skilled workforce, and creating a culture of innovation. The time is now for manufacturers to embrace this transformative technology. Let’s talk!