Machine failures undermine streamlined processes, delay production, deteriorate customer service, and lead to huge costs. According to the True Cost of Downtime report, Fortune Global 500 manufacturers lose around 3.3 million hours per year because of poor condition monitoring.
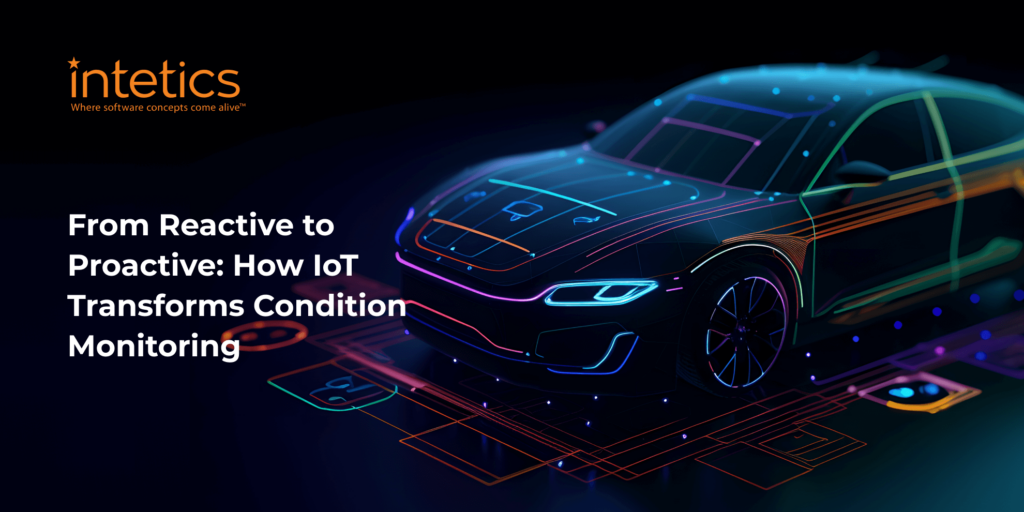
This, in turn, costs them $860 billion or 8% of their annual revenues. Other findings by Senseye, a machine health management company, suggest that one hour of unplanned downtime costs a business $532,000, and large facilities lose around 27 hours monthly, which is almost $14.4 millions of wastage.
The problem can be anticipated with predictive analytics, which is fostered by advanced condition monitoring systems. Today, they are powered by IoT (Internet of Things), which enables real-time access to numerous sensors that monitor the state of equipment to forecast its possible failures.
Condition Monitoring Systems: Definition and Evolution
Condition monitoring of machines implies constant supervision of the conditions in critical machinery while they are in operation. As a result, it allows businesses to timely identify changes that may result in a fault or malfunction. This ability aids in predictive maintenance.
Read also: What Is Predictive Maintenance?
Traditionally, the process has been performed manually: a responsible on-site employee would monitor the state of conditions of the industrial machines, following a specific frequency. However, the approach isn’t efficient, especially with the growing production needs and client expectations. Therefore, companies often fail to provide a complex overview of the conditions throughout the facility, face unplanned downtimes, and experience unwanted costs.
The viable solution is DAQ, or data acquisition software, that measures electrical or physical phenomena like voltage, current, temperature, sound, or pressure through sensors and DAQ measurements hardware/software. It allows for permanent condition-monitoring of rotating machinery (like fans, blowers, motors, or gearboxes) across several industries, including automotive, chemical, construction, power generation, mining, oil & gas, and more.
To meet the need for an efficient approach, condition monitoring services are being promoted. The market for such services is expected to steadily grow at a CAGR of over 7% by 2030, according to Grand View Research. The analysts claim that solutions allow manufacturers to optimize and monitor the performance and maintenance of their equipment. What is more, it aligns with the trend for lean manufacturing, which implies waste minimization at maximum productivity. Condition monitoring leads to increased production efficiency, reduced downtime, and cost prediction. Here’s a summary of its benefits:
- Enhanced asset performance. By timely identifying changes in equipment conditions, businesses can opt for proactive maintenance, reduce the number of faults, and improve asset performance.
- Reduced maintenance costs. Condition monitoring for equipment is like a regular check-up for a human. It’s easier and cheaper to maintain proper health levels when taking care of yourself before getting sick.
- Extended asset lifespan. Machinery is likely to serve you longer if it’s taken care of. This implies ensuring proper conditioning and proactive (rather than reactive) maintenance.
- Improved operational efficiency. By reducing the amount of unplanned downtime, you can decrease stress factors that undermine your streamlined production and reduce efficiency.
The Internet of Things (IoT) and Its Role in Condition Monitoring
IoT empowers more accurate and efficient monitoring; it also allows for remote condition monitoring, which is especially relevant for those deploying machines in extreme conditions. Here’s a brief overview of the technology’s applications:
- Sensors for condition monitoring are installed on a machine. Since every piece of equipment is different, it’s essential to retrofit or modify it before the installation to ensure proper sensor performance. It’s best to set up an efficient collaboration between a plant manager and a vendor installation team.
- Sensors collect a variety of data, determining the equipment’s performance and health. Some variables include temperature, vibration frequency, and pressure. You can even install a velocity sensor (a device that measures the change in distance over time) or an accelerometer (a device to measure static or dynamic acceleration).
- The collected data (or the measurement) is transmitted to the cloud, where it’s then aggregated in a database. This allows you to easily access it without any limitation; it can also be further processed to optimize costs and improve overall productivity through data-driven insights.
- If you implement AI (artificial intelligence) and ML (machine learning) algorithms, they can automate your condition monitoring, foster data analysis, and enable real-time alerting.
Download White Paper: ML Models: Exclusive AI/ML Knowledge for Business and Engineers
Let’s examine the last point in detail, as it’s among the top reasons why businesses choose IoT-based condition monitoring.
AI and ML technologies:
- Apply various analytical tools to provide informative reports on real-time machinery conditions, as well as predict possible downtime. This will allow you to proactively carry out maintenance and prevent unexpected failures.
- Enable you to start tracking remote quality control; for example, sensors can analyze if the quality of produced paper is good based on the condition of roll presses.
- Allow you to receive real-time alerts on current deteriorations. The 24/7 analysis constantly monitors the conditions of your equipment, immediately sending the responsible party an alert if it deteriorates or fails, or if its state reaches critical conditions.
4 Benefits of IoT-Based Condition Monitoring
Here are the main benefits you will reap if you invest in IoT-enabled condition monitoring:
1. Proactive and Predictive Maintenance
Traditionally, businesses apply reactive maintenance: the equipment is fixed after it breaks down. This results in unplanned downtime, which undermines the workflow and reduces productivity. Often, businesses try to avoid such a scenario with over-maintenance; they set up frequent, often unnecessary maintenance, which leads to the same outcome.
By analyzing sensor data, AI/ML-enabled analytical systems can timely notify you about deterioration and forecast potential failures. This allows you to quickly get rid of the problem unless it leads to a production collapse. What is more, you can optimize maintenance schedules to efficiently allocate resources.
2. Reduced Downtime and Maintenance Costs
Since the features of an automated analytical system allow you to forecast potential outages, you can minimize them, fostering more streamlined operations. This also allows you to invest less, as regular maintenance is often more affordable than full repair of critical equipment.
3. Enhanced Asset Performance and Lifespan
By collecting sensor data and transmitting it to reliable cloud storage, from where it’s used by AI/ML algorithms, you can get a 360-degree view of the state of your industrial machinery. Real-time condition monitoring that fosters predictive maintenance allows you to improve the overall state of equipment in real-time, therefore boosting its performance and lifespan.
What is more, you can rely on data-driven insights when making decisions about asset replacement or refurbishment. You won’t risk getting rid of still-performant expensive equipment thanks to comprehensive data analysis.
4. Improved Safety and Risk Management
Failure to timely detect hazardous conditions often results not only in extra costs but also in increased production risks that may involve the employees’ well-being. Occasional catastrophic breakdowns due to maintenance gaps increase employees’ exposure to hazardous conditions and may lead to potential environmental disasters. With IoT-based condition monitoring, you will be able to set up risk management to improve the safety at workplace.
Challenges of IoT-Based Condition Monitoring
Although IoT-based remote condition monitoring is an efficient and cost-effective solution, businesses often face three common challenges when implementing it:
- Technological. To collect accurate and complete data, you need to correctly install sensors on your equipment. Besides this, you need to establish real-time data exchange between sensors, cloud databases, and your internal systems where analytics are applied. Network connectivity and bandwidth constraints are some problems that often occur. They may be addressed with solutions like EtherCAT.
- Data management. To ensure data accuracy and consistency, it’s not enough to set up correct sensor performance. It’s also essential to correctly identify the types of data you need to collect in order to timely detect malfunctions of specific machinery. What is more, you need to set up reliable data sharing and storage to protect your intellectual property.
- Organizational. The global digital skills shortage is a common problem businesses face with the increasing pace of digital automation. Besides the lack of relevant skills to enable enhanced productivity through tech deployment, employees often resist change, which prevents businesses from quickly implementing advanced solutions.
How Are IoT-Based Condition Monitoring Systems Applied?
Advanced condition monitoring solutions are used in various industries, including:
- Automotive — to automate tracking of the state of laser drilling machines or welding machines.
- Steel — to control the state of cold rolling mills that directly affect the quality of products and are hard to inspect.
- Oil and gas — to monitor drilling equipment, pipelines, storage tanks, and other constructs.
- Construction — to track the operations of heavy machinery.
Future Outlook: Emerging Trends and Opportunities in IoT-Enabled Condition Monitoring
IoT, as a key driver of advanced automated condition monitoring, is likely to provide businesses with higher-quality outputs with the rise of 5G connectivity. It’s expected to provide enhanced mobile broadband, thereby facilitating data transmission. Furthermore, when integrated with AR, it can allow for thorough remote inspections, improving the quality of monitoring, while the digital twin technology can aid in forecasting change at a plant.
Summing Up
Conditional monitoring allows you to minimize unplanned downtime, which reduces unexpected costs and delays. To foster real-time 24/7 monitoring, businesses opt for IoT-enabled conditional monitoring. This allows for predictive maintenance, risk management, and reduced downtime and maintenance costs, as well as improved asset performance and a longer lifespan. All this is possible because of real-time alerts in the case of equipment deterioration and data analysis forecasting potential failures.
Those who have already applied IoT-based conditional monitoring are gaining a competitive advantage by providing stable quality even in times of uncertainty. This is especially relevant considering the increasing customer demands. In the future, automated condition monitoring with forecasting features will be the backbone of streamlined operations at industrial facilities.
Looking for designing & implementing IoT-based condition monitoring system in your operations? Get a free consultation now!